ADVANTAGES OF THE SYSTEM:
Reduction in Liquid and Coating Consumption: Precise Application: The system reduces liquid and coating consumption by covering only the targeted product, eliminating excess spraying. This leads to cost savings.
Uniform Coating on Complex Shapes: Consistent Application: Parts with unusual shapes are coated uniformly, even in hard-to-reach areas. Regular application improves overall product quality by reducing rejected items, reprocessing, and minimizing scrap.
Increased Operational Flexibility and Cost Savings: Elimination of Fixed Product Placement Need: The system eliminates the need for fixed product placement and single-product operation on carriers. Operators can mix and match products without the need for expensive tooling equipment and changes to spray setups, contributing to cost savings.
Low Labor Costs: Higher Level of Automation: The system enables a higher level of automation in various operations, resulting in a decrease in labor costs. By automating repetitive tasks, operators can focus on the more complex and value-added aspects of the production process.
In summary, the integration of the described system brings effective use of liquids and coatings, consistent coating for different part shapes, increased operational flexibility, cost savings by eliminating the need for fixed product placement, and reduced labor costs through increased automation. These advantages contribute to an optimized and streamlined production process.
IDEAL APPLICATION AREAS:
Application of Costly Liquids in Unwanted Waste Situations: Ideal for applying costly liquids in unwanted waste situations. The system minimizes waste probability, allowing efficient use of expensive liquids.
Coating Application on Objects with Unusual Shapes: Suitable for coating objects with unusual shapes. The system can consistently coat products with complex shapes, enhancing overall product quality.
Coating Application on Products of Different Sizes and Shapes on Conveyors: Ideal for coating products of different sizes and shapes on conveyors, providing flexibility to operators by eliminating the need for fixed product placement.
Coating Application on Products in Changing Positions on Conveyors: Suitable for coating products in changing positions on conveyors. The system ensures uniform coating even when products have variable positions on the conveyor.
Liquid Application on High-Speed Indexing or Continuous Conveyors: Suitable for applying liquid on high-speed indexing or continuous conveyors. It provides precise and efficient coating even during rapid product transitions.
Coating, Drying, and Air Blowing Applications: Suitable for coating, drying, and air blowing applications in industries such as automotive, food, metal processing, plastic/rubber, and others.
These features demonstrate that the system is ideal for use in various industries, particularly emphasizing effective use of costly liquids, coating of products with different shapes, and flexibility in conveyor systems.
ADVANTAGES:
Strong and Directed Airflow: WindJet® air nozzles provide a powerful and directed airflow for effective and efficient drying and blowing applications. It ensures a dryer result even on surfaces with cracks and crevices.
Enhanced Safety: WindJet® air nozzles are equipped with a protection edge to prevent blockage of the air outlet, increasing safety.
Up to 60% Reduction in Perceived Noise Level: For example, an open pipe at 7 bar pressure produces a measurable 98 dBa noise level, while a WindJet® air nozzle produces only 85 dBa. This results in a 13 dBa reduction and up to a 60% decrease in perceived noise level.
Uniform Air Curtain with Balanced Impact Distribution: Mounting multiple WindJet® air nozzles on a header creates a uniform air curtain with balanced impact distribution. This ensures consistent drying or blowing processes.
Suitable for Food Contact Applications: WindJet® air nozzles are now available in a new PVDF material for Food Contact applications, complying with EC10/2011, EC1935/2004, and FDA standards. The material includes a metal-detectable component, providing a significant safety advantage over other plastic materials. Even small particles of this plastic material are detectable.
TECHNICAL SPECIFICATIONS:
Low Noise Level: It has a low noise level.
Various Application Possibilities: It offers various application possibilities.
4 Different Material Options: ABS (Acrylonitrile-Butadiene-Styrene) PPS (Polyphenylene Sulfide) SS (Stainless Steel AISI 316) PVDF material for Food Contact applications (EC10/2011, EC1935/2004, FDA) with metal-detectable feature.
1/4" BSPT Threaded Connection:
Usable up to 400°C (SS): Usable up to 400°C with SS material.
Maximum Pressure: Up to a maximum of 7 bar pressure for plastic materials. Up to a maximum of 10 bar pressure for SS.
Excellent Chemical Resistance: Excellent chemical resistance in PPS, PVDF, and SS materials.
Efficient Air Consumption and High Impact Force: Efficient air consumption with high impact force.
Additional Mounting Hole for Fixation: It has an additional mounting hole for fixation.
Full Headers (Connection Parts) Available in Different Lengths and Materials: Full headers are available in different lengths and materials.
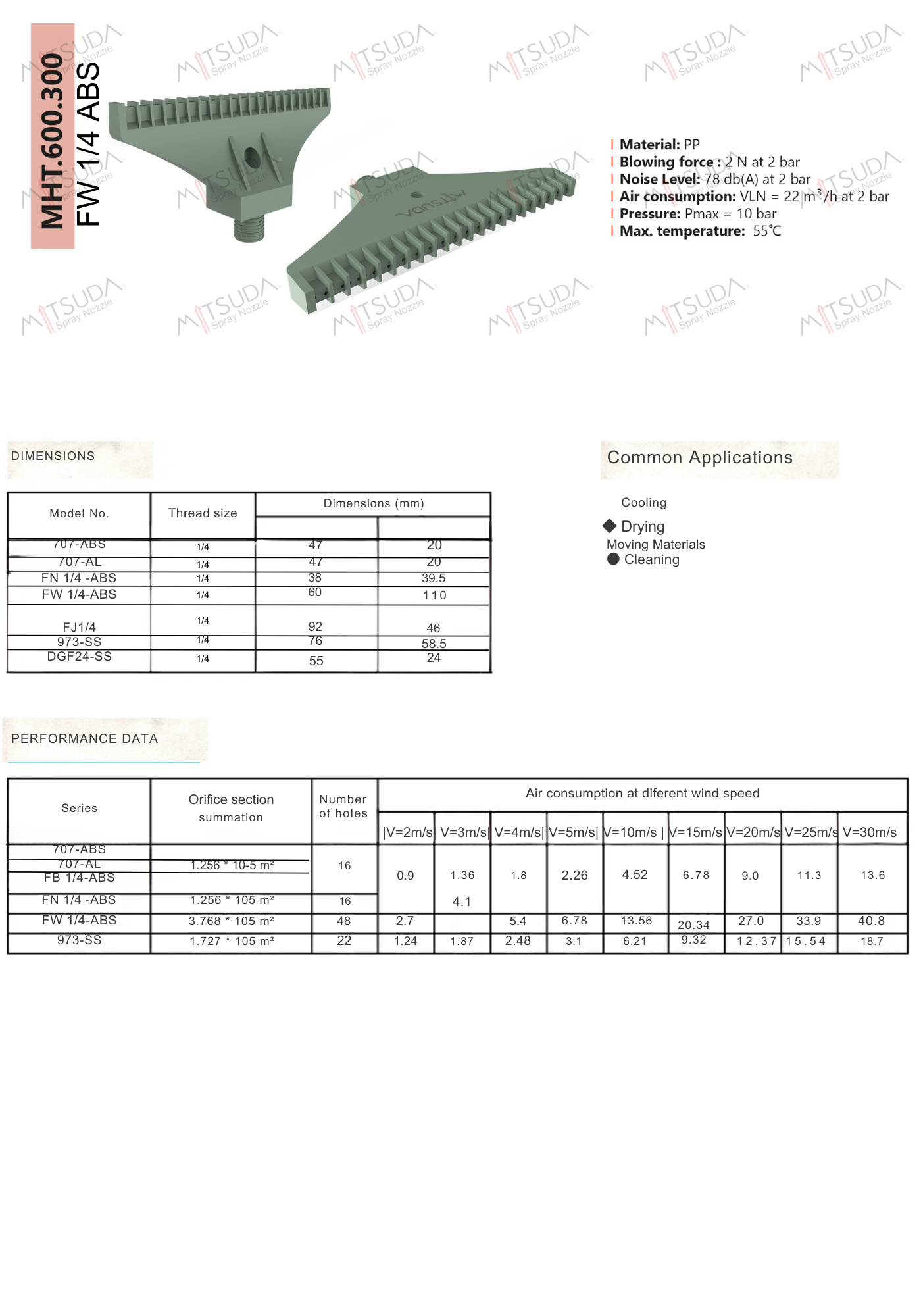